What quality management practices are needed to achieve excellence, again and again?
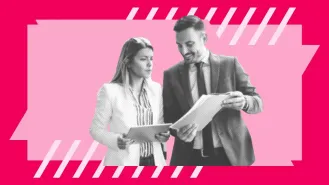
Today, more than ever, companies must use strategies to stand out from the crowd and make themselves memorable in the minds of volatile consumers. Consumers are spoilt for choice, and given the same conditions of access to products or services (particularly in terms of price), they will naturally turn to the most qualitative offer.
With this in mind, organizations are realizing the benefits of introducing a quality management process, with the aim of generating value and customer satisfaction.
A number of standards are used to achieve this, starting with ISO 9001, which lays down the main principles of the QMS ( Quality Management System). In this article, we take a closer look at these key principles, with the added bonus of advice and tools to help you put them into practice.
Definition of quality management
What is Quality Management?
Quality Management (QM) refers to all practices designed to ensure the quality of a company' s products and services, in line with the expectations of its stakeholders. This quest for quality touches on various dimensions, in particular :
- production;
- customer satisfaction
- internal processes;
- human resources;
- regulatory compliance;
- profitability.
What is the main objective of quality management? To offer consumers the best possible experience , while taking into account time and cost constraints. At the same time, faced with ever more stringent regulations, QM addresses compliance issues.
Quality management is strongly associated with QMS ( Quality Management System), which is akin to a documented and standardized tool (where QM constitutes a more global approach).
💡To wit: quality management often includes risk management, with a view to anticipating problems likely to affect the performance of procedures. Indeed, a proactive approach secures every step, and expenses linked to potential failures are reduced as a result!
👉 Diagram explaining the 4 types of quality:
Differences from quality assurance
While the two concepts remain closely related, quality management differs from quality assurance (QA). The latter focuses more on the proactive implementation of procedures designed to ensure compliance with predefined requirements.
The aim? To give consumers the confidence to turn to your brand rather than another.
Differences with quality control
Quality control (QC), on the other hand, is more reactionary.
It's about testing, checking that the product or service supplied meets the quality expectations agreed by industry standards, as well as your own objectives.
Of course, you'll need to make any necessary corrections afterwards.
☝️ In short, QC and QA are sub-processes of QM.
Importance and challenges of quality management
Acquiring and retaining customers
In the face of competitive pressure, it is often difficult to stand out from the crowd. Especially at a time when consumers are becoming ever more demanding!
To stand out from the crowd, and thus acquire and retain more customers over the long term, you need to be uncompromising about the quality of your products and/or services. This applies to all points of contact with consumers (customer service, production, etc.).
In short, you must constantly strive to improve the customer experience.
Comply with legal requirements
Another crucial issue is compliance with legal requirements and other standards.
And with good reason, all sectors are impacted by these kinds of obligations: marketing (and not only!) with the RGPD, the food industry with the Hygiene Package, etc.
By complying with regulations, you protect yourself from legal risks, and therefore from consequences (sometimes disastrous!) in terms of costs and reputation.
Increase your profitability
Finally, quality management has a direct impact on your organization's profitability.
By optimizing your internal processes (to reduce waste, limit errors, etc.), you cut costs and boost overall efficiency and productivity.
Add to this the increase in sales resulting from customer satisfaction, and you get a blissful balance that promises long-term growth.
What are the 7 principles of quality management?
Quality management: the ISO 9001 definition
Quality management remains strongly linked to compliance with quality standards, of which the best-known and recognized standard is ISO 9001, in its 2015 version.
ISO 9001 provides a structured framework for implementing a quality management system, and is based on 7 principles:
- customer orientation
- leadership;
- employee involvement;
- process approach;
- continuous improvement;
- evidence-based decision-making;
- stakeholder relations management.
👉 Let's review these 7 principles with the benefits to be gained, and examples of actions to be deployed.
Principle 1 - Customer focus
This principle aims to meet and exceed customer needs by delivering quality products or services.
👍 Benefits:
- increased customer loyalty and lasting customer satisfaction ;
- increased business opportunities;
- better understanding of market expectations.
⚙️ Actions to implement:
- organize satisfaction surveys;
- personalize your offer in line with your customers' wishes;
- maintain proactive and reactive communication with them.
Principle 2 - Leadership
This precept underlines the importance of strong management, with a clear vision. It's about fostering a culture of quality, committing the whole organization to common goals.
👍 Benefits:
- alignment of organizational objectives with the quality strategy ;
- increased team motivation;
- orientation of corporate culture towards quality.
⚙️ Actions to be implemented:
- define clear values and make them a reality;
- encourage exemplary leadership;
- set measurable qualitative objectives and monitor their progress (via OKRs, for example).
Principle 3 - Employee involvement
Quality depends on employee commitment. They must be given responsibility and encouraged to contribute actively to continuous improvement.
👍 Benefits:
- optimized operational efficiency ;
- skills development and talent enhancement;
- a positive work climate supporting innovation and collaboration.
⚙️ Actions to be implemented:
- plan quality awareness training courses;
- encourage recognition of individual and collective contributions;
- involve employees in problem-solving.
Principle 4 - Process approach
This principle advocates the interconnection of processes, in favor of efficient management of quality-related activities.
👍 Benefits:
- greater consistency in operations ;
- fewer errors and less waste ;
- better risk control.
⚙️ Actions to be implemented:
- map and document the organization's key processes;
- define performance indicators for each process;
- rationalize interactions between procedures.
Principle 5 - Continuous improvement
The constant quest for improvement guarantees the sustainability of the quality management system, even in the face of market developments and new regulatory requirements.
👍 Benefits :
- the ability to adapt to change, whatever the circumstances;
- maintaining profitability, even in the face of unforeseen events;
- enhanced competitiveness.
⚙️ Actions to be implemented:
- implement continuous improvement cycles (PDCA);
- analyze feedback to identify areas for improvement;
- encourage a culture of innovation.
Principle 6 - Evidence-based decision-making
All quality management decisions must be based on the analysis of reliable data, to ensure the relevance of the actions deployed.
👍 Benefits:
- decision-making in line with reality on the ground ;
- reduction of uncertainties and risks;
- continuous improvement based on concrete facts.
⚙️ Actions to be implemented:
- regularly collect data on processes and performance ;
- regularly analyze quality-related KPIs and make decisions based on these analyses;
- use specific tools, such as dashboards.
Principle 7 - Managing relations with interested parties
It's important to proactively manage relationships with the various quality-related stakeholders (customers, suppliers, partners, etc.) if you want to mutually generate value and satisfy your common interests.
👍 Benefits:
- strengthening trust with your partners ;
- supply chain optimization;
- better anticipation of stakeholder expectations.
⚙️ Actions to implement:
- understand the expectations of the various stakeholders involved;
- establish clear partnership agreements and commitments;
- communicate regularly and transparently with stakeholders.
How to set up a QMS, or Quality Management System?
QMS stands for Quality Management System, and refers to a standardized quality management system or process.
👉 Discover the steps to follow to set yours up:
Step 1 - Define company objectives and expectations
Like many operations, QMS starts with the definition of clear objectives, aligned with the company's overall strategy. In this way, you'll be able to identify the direction you need to take, and prioritize your actions accordingly.
To do this, you need to analyze the needs of your stakeholders. Customers, suppliers, employees... take into account the requirements of all of them, as well as those inherent in the applicable standards.
Once your expectations have been defined, formalize and communicate your quality policy to your teams.
Step 2 - Analyze existing systems and identify potential gaps
Before improving the existing system, you need to understand your strengths and weaknesses!
So it's a good idea to take an in-depth look at your current processes to identify any gaps with the objectives you've defined. Internal audits, interviews and data analysis are valuable tools in this respect.
💡 Tip : we recommend that you draw up a detailed process map. It will help you to better understand how your business operates, and therefore focus on the most critical areas.
Step 3 - Deploy your action plan
A structured action plan guides improvement operations by formalizing :
- the tasks to be carried out ;
- the people responsible;
- deadlines.
Bear in mind that each of these actions must have a measurable impact on quality. In addition, always prioritize initiatives according to their degree of relevance to the objectives set.
💡To know: the implementation of a QMS relies on the quality players within the organization. While, as we've seen, everyone has a role to play, certain stakeholders will have a greater influence on results. These include
- management: while quality management itself is delegated by management, it is management that elevates quality management to the status of a corporate value, and thus sets the wheels in motion. It also plays a major role in identifying strategic objectives.
- the quality management manager: quite simply, this is the conductor of the process, ensuring that everything runs smoothly.
- employees: yes, everyone, in their own way, contributes to the continuous improvement of quality management!
Quality management tools
There are a plethora of tools to support quality management! And for every link in your process chain.
We won't go into them all here, because we've already got a great article on the subject 😉 : 13 quality tools to control your projects and quickly identify risks.
Nevertheless, here's a (non-exhaustive) overview of these tools, by typology of need. 👉
To define and structure processes
- The various ISO standards (ISO 9001, ISO 14001, etc.) : these standards provide a structured framework for implementing your quality management system, ensuring its compliance with regulatory requirements and consumer expectations.
- SIPOC ( Suppliers, Inputs, Processes, Outputs, Customers): this tool is used to map a procedure by identifying suppliers, inputs, processes, outputs and customers. The aim? To provide a global view of these key quality components.
- Process mapping: graphically representing the different stages of a procedure, to visualize interactions, responsibilities and, consequently, opportunities for improvement.
To analyze and improve performance
- PDCA ( Plan, Do, Check, Act): also known as the Deming wheel, this cyclical method guides continuous improvement by structuring actions into four phases: planning, implementing, checking and adjusting.
- Pareto law (80/20): the Pareto law pinpoints the major causes of a problem, demonstrating that 80% of the effects come from 20% of the causes. This makes it easier to prioritize corrective actions.
- The 5M (Ishikawa diagram): this diagram helps to analyze the root causes of a problem by exploring five determining factors: material, method, environment, equipment and manpower.
To manage risks and non-conformities
- FMEA : this method assesses risks by detecting failure modes, their impact and criticality.
- SWOT matrix ( Strengths, Weaknesses, Opportunities, Threats): this strategic tool analyzes the internal and external factors (strengths, weaknesses, opportunities and threats) influencing an organization's performance.
- Non-conformity management plan: this involves understanding, documenting and then dealing with any deviations from requirements, in order to prevent their recurrence.
To monitor and measure quality
- Quality dashboards: these centralize key performance indicators (KPIs) designed to monitor the effectiveness of quality actions.
- Internal and external audits: these assessments verify the conformity of operations with internal criteria and standards.
- Quality checklists: these support systematic control of the company's product and service quality requirements.
Involving and mobilizing teams
- Brainstorming: this well-known technique stimulates collective intelligence and creativity. How does it work? By bringing teams together to brainstorm all possible ideas for solving a problem.
- The 5 Whys: this is a simple analysis tool that identifies the root cause of a problem by asking the question "Why? ".
- Quality training: these sessions are designed to enhance employees' skills and raise their awareness of good quality practices.
What about software?
Unsurprisingly, when it comes to tools dedicated to quality management (and any other company process after all), the question of software solutions quickly comes to the fore.
Various platforms have been developed to help you implement your QMS, by digitizing and streamlining your processes. In particular, they are used to collect and analyze all data in transit within the organization, to better document quality processes and direct associated actions.
🛠️ One example is Agilium SMQ, a quality management software package for SMEs. It enables you to efficiently structure and manage your quality procedures, with a wide range of functions: process mapping, risk management, audit and non-conformance supervision, supplier assessment, etc. Agilium SQM also optimizes the follow-up of corrective actions following the identification of your areas for improvement. All this through a fully customizable interface (BPM technology), capable of adapting to your own needs.
Finally, how do you choose your quality management software?
Convinced of the benefits of software to manage your Quality Management System? Let's end this article on a high note 🤩, by revealing the 5 criteria to consider when selecting the one that will find favor in your eyes:
- ✅ Aligning the solution with your needs. First and foremost, you need to opt for a tool with features that are perfectly aligned with your needs. And therefore compatible with the structure of your company, but also and above all with your sector of activity. Let's take the example of quality standards: they simply aren't the same depending on whether you work for a software publisher or in the pharmaceutical industry.
- ✅ Scalability and flexibility. In keeping with this logic of compliance with your specific requirements, your quality software must be able to support your own processes, but also your growth (and the increase in the amount of data that goes with it). And it must do so without turning your parameter changes into a gas factory!
- ✅ The power of technology. Beyond the scope of the functional coverage itself, it's appreciable that these features are enriched with the latest technologies, starting with artificial intelligence and machine learning. Among other things, they will enable you to gain valuable insights.
- ✅ Ergonomics. A platform's intuitiveness facilitates its adoption by teams and reduces resistance to change. Focus on the clarity of the interface, but also on the degree of customization of dashboards as well as the speed of access to critical data.
- ✅ Choice of provider. We advise you to use a recognized publisher, providing its customers with a responsive support service in the event of a problem. And it's even better if the solution has an active user community, synonymous with a wealth of online help and resources.
All that's left is to find the right software to structure your quality management procedure efficiently . Your brand will become a matter of course for consumers ✨.
Article translated from French

Currently Editorial Manager, Jennifer Montérémal joined the Appvizer team in 2019. Since then, she's been putting her expertise in web copywriting, copywriting and SEO optimization to work for the company, with her sights set on reader satisfaction 😀 !
Trained as a medievalist, Jennifer took a break from castles and manuscripts to discover her passion for content marketing. She took away from her studies the skills expected of a good copywriter: understanding and analyzing the subject, rendering the information, with a real mastery of the pen (without systematically resorting to a certain AI 🤫).
An anecdote about Jennifer? She distinguished herself at Appvizer with her karaoke skills and boundless knowledge of musical nanars 🎤.